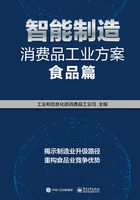
智能制造基本情况
一、智能制造项目技术特点
2016年,伊利集团探索建立首个乳品智能制造新模式示范项目,研发应用新一代装箱机器人、新一代码垛机器人、国产智能物流装备、生产过程管控系统、全生命周期质量追溯系统及配方管理系统,实现乳品工厂制造装备升级,建设信息互联互通的智能工厂。
本项目应用机器人、自动化等技术,突破了自动开箱、智能装箱、智能码垛、产品质量在线检测剔除等工艺难题,改变了传统手工作业方式,实现了二次包装智能化生产,提高了生产效率,降低了运营成本且保证了产品品质。

二、智能制造项目实施效果
AGV智能物流系统包括控制系统、自动引导系统、自动充电系统、运行监控系统及呼叫终端等。AGV控制系统主要由监控计算机、地面基站天线及定位反光板等设备组成。AGV监控计算机通过工业以太网与物流信息管理系统计算机进行通信,并与自动导引车通过无线局域网进行通信,实现过程控制。
设计乳品全生命周期质量追溯系统,在原奶、生产、流通、终端市场各环节实现产品质量全流程追溯;加入防错措施,提升产品品质。
通过生产计划分解、原辅料赋码、投料生产过程防错、产品及配方管理、设备运行记录、半成品追溯、报表管理等功能模块实现生产过程的管控。

产品追溯系统自产品包装开始,通过赋码、采集、关联、解析、入出库扫描等业务流程,应用OCR、PDA、数据库、网络传输等技术读取分析信息,与ERP、TMS、WMS、云商大数据平台实时交互信息,可实现产品从生产到终端市场的正向追踪、反向追溯及防窜货管控,进而提升产品品质、促进企业的精细化管理。
MES与APS、BI、WMS、SRM、分销系统进行关联监控与分析,避免计划与执行、信息与决策的脱节。
通过信息化与自动化融合,解决了企业“信息孤岛”问题,取消纸质报表,实现数据高效、准确采集和分析,提供过程控制依据、管理决策依据,实现生产成本的大幅度降低。
提升乳品二次包装设备的自动化与智能化水平,提升国产装备占比;集成乳品全生命周期质量追溯系统、配方管理系统、智能物流系统;与协同合作方组建联合体,建立项目管理机制;打造示范样板,建立企业及行业标准。解决了企业长期存在的手工作业效率低的问题、生产加工过程的准确性低导致生产运营成本高的问题、产品在生产过程中的质量隐患难追溯的问题、生产过程中设备停机清洗导致的能源浪费问题。
通过项目实施,解决了生产制造中的很多关键问题,例如,突破高端产品自动装箱、包装辅料自动插入及小箱自动扣盖等技术难题;引进OCR视觉系统,实现最小包装到托盘的四级关联、二维码(QR)变码在线喷印和检查;突破小箱装大箱的技术难题,有效降低人员劳动强度;改善生产过程中多品种、多规格装箱问题(如3×4、3×8、4×5、2×3×2等不同的装箱规格),实现快速切换功能;通过网络系统和中控系统关联,实现信息远程传递和监控。
三、存在的问题和改进的方向
当前,智能制造的发展还面临一些问题,我国智能制造装备关键元部件主要依赖进口(如工业机器人的高性能交流伺服电机和高精密减速器),智能制造诸多基础技术仍然停留在仿制层面,创新能力不足,关键技术难以突破,导致国产智能制造企业成本居高不下;从整体上看,我国智能制造产业强调智能生产和智能制造服务,忽视智能管理、智能设计环节,使得智能制造某些核心技术处于实验室阶段,制约了产业化进程。
智能制造建立在自动化、机器人、人工智能、云计算、物联网等一大批高新技术的综合运用上,找寻合适的技术源来改造企业生产模式成为智能制造成功的关键要素;智能制造领域技术门槛较高,仅仅依靠单个企业探索全新领域显然很困难。工业级产品对数字技术、智能技术、网络技术和新材料技术等方面要求很高,整体研发耗时较长。我国现有的智能制造技术大多掌握在科研机构手中,而多数研究机构过于独立封闭,技术研发分散,未能形成合力,同一技术重复研究,浪费了大量的研发经费和研发时间。